A Truly Collaborative Solid State Battery Scale-up Program
Posted on: in Blog
Programme SiSTEM has just ended, and it is now time to reflect on the findings of the last 18 months. SiSTEM was a collaboration between Ilika, Agratas, Mpac and the UK Battery Industrialisation Centre (UKBIC). The programme was funded by the UK Automotive Transformation Fund (ATF) and aimed at taking Ilika’s solid state battery (SSB) technology Goliath nearer to industrialisation. We are pleased to report that representatives of UK funding bodies Innovate UK and Advanced Propulsion Centre (APC) announced during the programme close-out meeting last week, that the consortium had passed expectations with flying colours and that SiSTEM was a glowing example of successful collaboration within the UK automotive ecosystem.
SiSTEM was yet another example of the productive collaborations Ilika now has with industrial equipment vendors, tool suppliers, factory automation specialists, and manufacturing scale-up facilities. This series of programmes showcase that there is no significant barrier to adopting oxide-based SSB technology such as Goliath, in manufacturing facilities currently producing lithium-ion batteries (LIB). In fact we previously reported, in a collaboration with robotics specialists Comau in 2021 (now part of Stellantis) that the majority (2/3) of equipment and processes were identical. As expected, SiSTEM further demonstrated that the deployment of Ilika’s SSB technology could be realised with confidence.
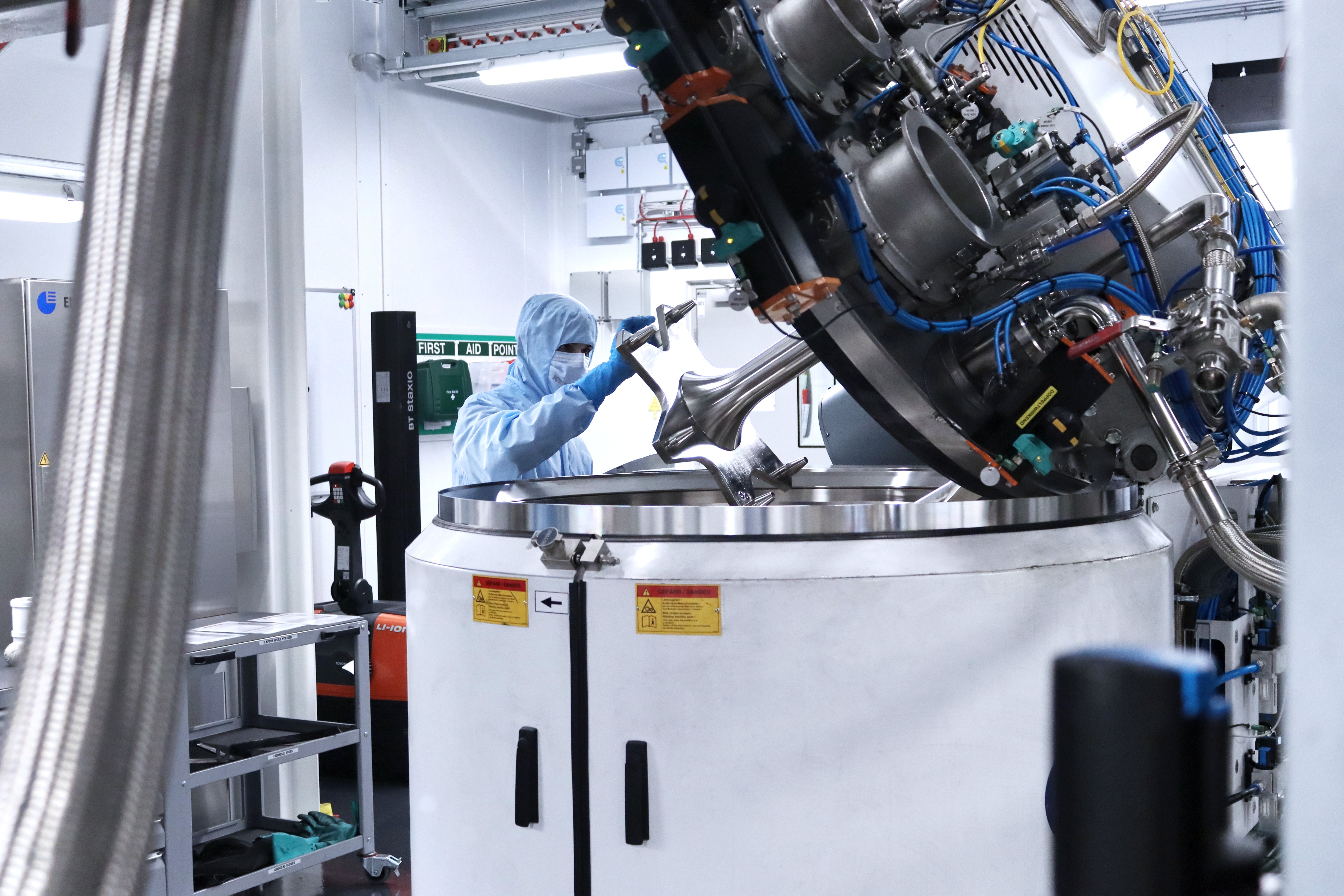
UKBIC is a battery development facility which provides manufacturing scale-up and industrially-recognised equipment also used in lithium-ion battery gigafactories. During SiSTEM, Ilika trialled large-scale preparation equipment and demonstrated roll-to-roll coating of its proprietary composite electrolyte-electrode. Other trials included calendering, slitting and notching, all with fantastic support and friendly guidance from UKBIC. The general conclusion was that all trials were successful!
Double-sided coating provided defect-free films with high yield, good reproducibility, clean edges and excellent cross-web profiles (a measure of flatness over the width of the films). There was no compatibility and sustainability issue with the solvents used. The slot die head used was commonly available and the current collectors were as thin as those used in most leading-edge LIB gigafactories. The cherry on the cake is that, when Ilika brought these materials back to its pilot line and built a batch of solid state 10Ah prototype cells, the results were superior in performance to those made with similar starting materials on Ilika’s pilot line, confirming that the tolerances of industrial equipment will unlock further improvements to Goliath SSB technology. The superior performance was measured as higher battery capacity under rapid charging protocols.
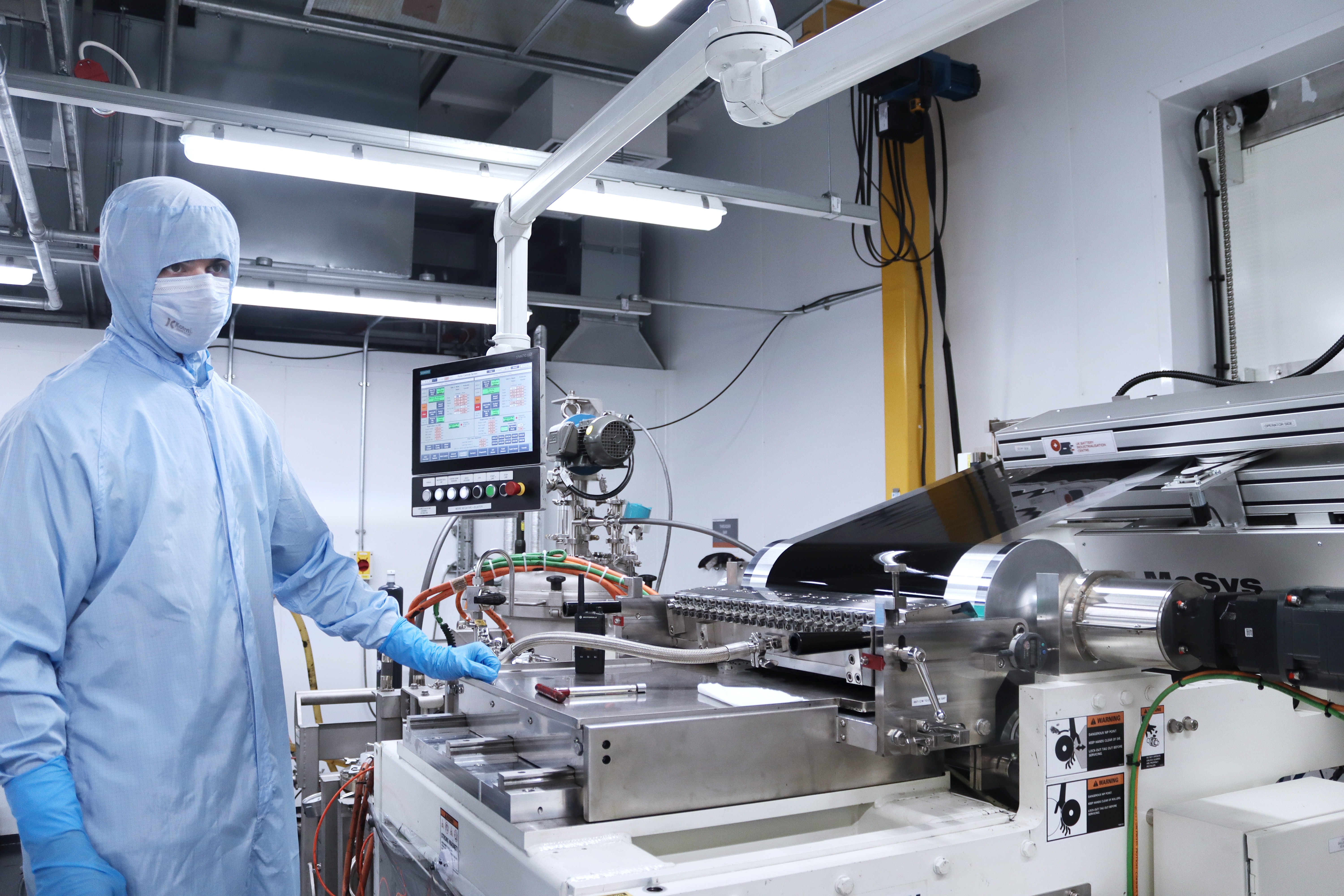
The Comau study did highlight that some LIB manufacturing equipment needs modifications to be used with SSB. This is exactly what Mpac did in SiSTEM: they modelled, designed and built a fully functional assembly robot. To simplify, assembly is the stage that comes straight after the stages demonstrated at UKBIC. Coated films are handled and stacked, ready for insertion in the cell pouch packaging. This equipment is fully automated and designed with the highest tolerance and precision required from a piece of equipment and is fully compatible with current LIB production equipment. All this takes place at speed, in order to match production throughput expected from Ilika’s 1.5 MWh A-sample pilot line where the equipment will soon be shipped. Mpac is a world-leading assembly & packaging automation company, active in many industries, now successfully demonstrating the expertise and performance of their products in the battery industry. Working with Mpac was truly collaborative and a great experience.
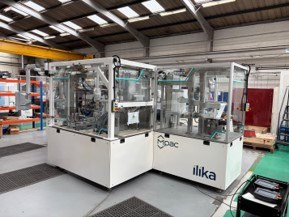
Last but not least, Agratas joined the consortium to understand the requirements for building a SSB prototype line, based on Ilika’s experience. A gap analysis study focused on compatibility aspects between Agratas lines and potential future SSB additions. This study included a concept facility design for the implementation of solid state battery manufacturing equipment at Gigafactory scale, focusing on formulations, equipment and processes alignment. Agratas is Tata Group’s global battery business created to design, develop and manufacture high-quality, high-performance, sustainable batteries in the mobility and energy sectors, including for anchor customers Tata Motors and JLR. Collaborating with Agratas in SiSTEM was rewarding and confirmed their previously-stated belief that “solid state is a very promising future battery technology”.
SiSTEM was a 18-month program which truly turned project partners into friends. This is hopefully only the beginning of Ilika’s working relationship with Agratas, UKBIC and Mpac!